壓裂車活動(dòng)彎頭爆裂分析!
發(fā)布時(shí)間:2019/02/15 點(diǎn)擊量:
某油田在一次打井操作中,用于壓裂車上的一只3"(76. 2 mm)105 MPa-50型活動(dòng)彎頭在壓裂作業(yè)時(shí)突然發(fā)生爆裂。
該活動(dòng)彎頭材質(zhì)為20CrNiMo,僅使用1年左右。經(jīng)復(fù)驗(yàn),其化學(xué)成分符合標(biāo)準(zhǔn)要求。彎頭生產(chǎn)工藝流程為:鍛件一正火一粗加工一滲碳淬火一低溫回火一機(jī)加工,出廠前按《高壓流體控制產(chǎn)品出廠實(shí)驗(yàn)程序》的要求進(jìn)行過壓力值為158MPa的本體強(qiáng)度實(shí)驗(yàn),實(shí)驗(yàn)結(jié)果符合要求。
在壓裂作業(yè)時(shí)彎頭接觸的介質(zhì)為酸化液(20%的HC1+1.5%的HF+粘合劑),打一口井的酸化壓裂要壓入的酸性介質(zhì)體積在400m3到1000m3;,壓裂的壓力在50-90 MPa之間。為確定爆裂原因,對(duì)該泄漏管進(jìn)行取樣分析,本文介紹分析過程及結(jié)果。
1.檢驗(yàn)結(jié)果
1. 1宏觀檢查
圖1為拼復(fù)的爆裂彎頭宏觀照片。斷口銹蝕嚴(yán)重,但脆性斷裂特征仍十分明顯,圖2為彎頭橫向斷裂面,屬主要斷裂面。從圖中可以看出,斷裂發(fā)生在密封止口處,比較明顯的斷裂源有3個(gè),如圖2箭頭所示的A,B,C 3個(gè)部位。
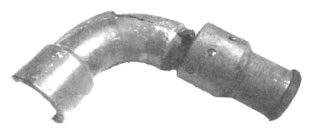
圖1破裂彎頭宏觀照片
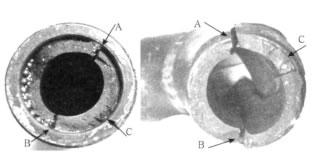
圖2破裂彎頭匹配斷口特征
A區(qū):有一條穿透壁厚的縱裂紋,縱裂面覆蓋一層嚴(yán)重的腐蝕產(chǎn)物,用熱鹽酸水溶液清洗后斷口形貌如圖3所示??v裂面斷口分為2個(gè)較明顯的區(qū)域:靠?jī)?nèi)壁一側(cè)較平坦,放射狀花樣從內(nèi)壁表面向壁厚方向擴(kuò)展,表明裂紋起源于內(nèi)壁;靠外壁一側(cè)斷口較粗糙呈纖維狀,該區(qū)域是最后撕裂區(qū)。同時(shí)在內(nèi)壁表面發(fā)現(xiàn)多條縱向微裂紋,可見該縱裂紋的形成與內(nèi)壁表面微裂紋相關(guān)。
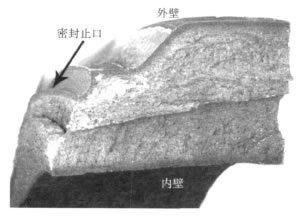
圖3 A部位縱裂縫斷而形貌
B區(qū):與A區(qū)特征大致相同。
C區(qū):該區(qū)約占整個(gè)斷面1/ 5,斷面上有多個(gè)層狀小平臺(tái),平臺(tái)上有明顯的放射狀條紋,條紋收斂于外側(cè)的密封止口底部,該處壁厚較薄。
根據(jù)上述特征可以看出斷裂的發(fā)展順序?yàn)?A,B內(nèi)壁表面微裂紋向縱、橫向擴(kuò)展,當(dāng)擴(kuò)展到一定程度,在C部位密封止口底部產(chǎn)生橫裂紋,最終產(chǎn)生橫向斷裂。
1. 2金相檢驗(yàn)
宏觀檢查發(fā)現(xiàn),圖2所示的A,B部位內(nèi)壁表面有多條縱向微裂紋,磨制其內(nèi)壁表面觀察到裂紋處及其附近有一些腐蝕坑,這些腐蝕坑常萌生于硫化物夾雜處(見圖4)。通過腐蝕坑底取橫截面金相試樣,裂紋呈鋸齒狀沿彎頭厚度方向擴(kuò)展,其內(nèi)有腐蝕產(chǎn)物,尾端??梢娏蚧飱A雜。
取縱截面金相試樣觀察,細(xì)條狀硫化物夾雜頗多(見圖5),按G B/ T 10561- 2005標(biāo)準(zhǔn)評(píng)定為A3級(jí)。
經(jīng)測(cè)量,試樣內(nèi)、外壁滲碳層深度為1. 2一1.4 mm,符合相關(guān)技術(shù)條件要求。
試樣內(nèi)、外壁表層組織均為粗片狀回火馬氏體+殘余奧氏體,原奧氏體晶粒度為8級(jí),裂紋沿奧氏體晶界擴(kuò)展(見圖6),終止于滲碳層內(nèi)部;心部為馬氏體與貝氏體的回火組織。
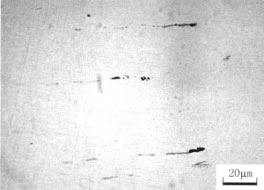
圖4內(nèi)壁表而硫化物夾雜與腐蝕坑
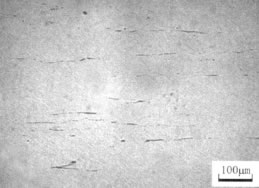
圖5截面試樣硫化物夾雜
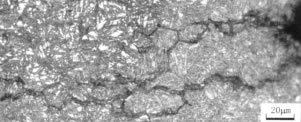
圖6裂紋沿奧氏體晶界擴(kuò)展
1. 3掃描電鏡觀察
用掃描電鏡對(duì)圖2所示的主斷口和A,B部位縱裂面進(jìn)行分析,斷口覆蓋有腐蝕產(chǎn)物,腐蝕產(chǎn)物中富集C1元素(w (C1)=17. 11%)見圖7。
用丙酮溶液清洗去掉主斷口腐蝕物后觀察,彎管內(nèi)、外壁表層(深度約0. 84 mm的范圍)以沿晶斷裂為主,局部有二次沿晶裂紋,顯示出明顯的冰糖狀花樣,見圖8。其余部位為準(zhǔn)解理+解理特征,并有少量細(xì)小二次裂紋。
用掃描電鏡能譜分析儀對(duì)金相試樣進(jìn)行分析,內(nèi)壁表層腐蝕坑內(nèi)除Fe, Si的氧化物外,還富集有氯元素和少量硫元素(圖9);裂紋尾端分叉,其內(nèi)也富集氯元素(見圖10);裂紋尾端硫化物為硫化錳,夾雜中亦富集氯元素(見圖11)。
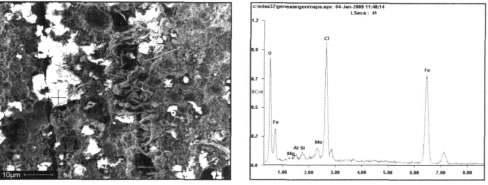
圖7斷口腐蝕產(chǎn)物能譜分析圖
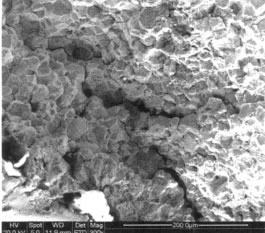
圖8外壁表層沿晶斷口及二次裂紋特征
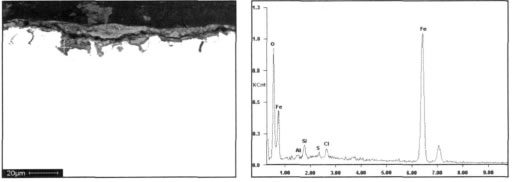
圖9截面內(nèi)壁表層腐蝕坑形貌及能譜分析圖
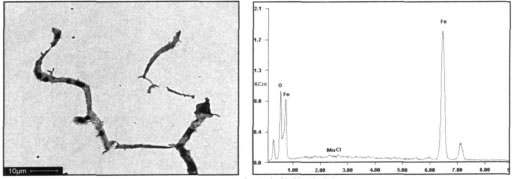
圖10裂紋內(nèi)腐蝕產(chǎn)物能譜分析圖
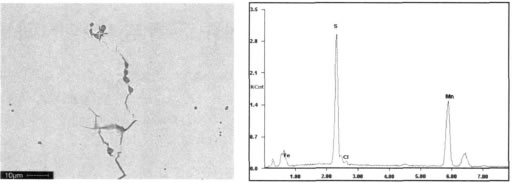
圖11裂紋尾端硫化物夾雜及能譜分析圖
2.結(jié)果分析
根據(jù)上述檢驗(yàn)結(jié)果,可認(rèn)為某油田壓裂車上的活動(dòng)彎頭在壓裂作業(yè)時(shí)發(fā)生爆裂事故,屬于應(yīng)力腐蝕破裂。
應(yīng)力腐蝕破裂是金屬構(gòu)件在拉應(yīng)力(外應(yīng)力或殘余應(yīng)力)和腐蝕介質(zhì)的共同作用下,引起的一種破壞形式。分析引起爆裂的因素如下:
1)掃描電鏡能譜分析結(jié)果表明,在彎頭內(nèi)壁腐蝕坑內(nèi)、裂紋中及硫化錳夾雜處均富集氯元素,沿晶破壞是應(yīng)力腐蝕破壞的一個(gè)特征,這說明引起彎頭應(yīng)力腐蝕的介質(zhì)是氯化物,它是一種很強(qiáng)的應(yīng)力腐蝕介質(zhì)。該活動(dòng)彎頭僅使用1年左右,接觸的介質(zhì)為酸化液(20%的HC1+1.5%的HF+粘合劑),可見氯化物來源于酸化液中的HCI。
2)打一口井的酸化壓裂要壓入的酸性介質(zhì)體積在400 m3到1 000 m3,壓裂的壓力在50 ~ 90MPa之間。因此,活動(dòng)彎頭在工作過程中要承受很大的拉應(yīng)力,為應(yīng)力腐蝕提供了應(yīng)力方面的條件。
3)該活動(dòng)彎頭材質(zhì)為20C rN iMo、其化學(xué)成分、機(jī)械性能均符合有關(guān)標(biāo)準(zhǔn)的要求。金相檢驗(yàn)結(jié)果表明,材料中硫化錳夾雜頗多,按GB/ T 10561-2005標(biāo)準(zhǔn)評(píng)定達(dá)到了A3級(jí)。這表明該鋼的純凈度較差,夾雜物數(shù)量較多會(huì)顯著降低鋼的耐應(yīng)力腐蝕性能。從金相檢驗(yàn)中發(fā)現(xiàn),腐蝕坑產(chǎn)生于硫化錳夾雜處,而裂紋萌生于腐蝕坑底部,可見活動(dòng)彎頭材質(zhì)中嚴(yán)重的硫化錳夾雜是應(yīng)力腐蝕裂紋的誘發(fā)點(diǎn),它是促使應(yīng)力腐蝕、破壞的因素之一。
3.結(jié)語
某油田壓裂車上的活動(dòng)彎頭在壓裂作業(yè)時(shí)發(fā)生爆裂屬于應(yīng)力腐蝕破裂。由于材質(zhì)中存在嚴(yán)重的硫化錳夾雜,在拉應(yīng)力及氯化物腐蝕介質(zhì)的作用下,由硫化錳夾雜處誘發(fā)的腐蝕裂紋進(jìn)一步擴(kuò)展即造成活動(dòng)彎頭破裂。
該活動(dòng)彎頭材質(zhì)為20CrNiMo,僅使用1年左右。經(jīng)復(fù)驗(yàn),其化學(xué)成分符合標(biāo)準(zhǔn)要求。彎頭生產(chǎn)工藝流程為:鍛件一正火一粗加工一滲碳淬火一低溫回火一機(jī)加工,出廠前按《高壓流體控制產(chǎn)品出廠實(shí)驗(yàn)程序》的要求進(jìn)行過壓力值為158MPa的本體強(qiáng)度實(shí)驗(yàn),實(shí)驗(yàn)結(jié)果符合要求。
在壓裂作業(yè)時(shí)彎頭接觸的介質(zhì)為酸化液(20%的HC1+1.5%的HF+粘合劑),打一口井的酸化壓裂要壓入的酸性介質(zhì)體積在400m3到1000m3;,壓裂的壓力在50-90 MPa之間。為確定爆裂原因,對(duì)該泄漏管進(jìn)行取樣分析,本文介紹分析過程及結(jié)果。
1.檢驗(yàn)結(jié)果
1. 1宏觀檢查
圖1為拼復(fù)的爆裂彎頭宏觀照片。斷口銹蝕嚴(yán)重,但脆性斷裂特征仍十分明顯,圖2為彎頭橫向斷裂面,屬主要斷裂面。從圖中可以看出,斷裂發(fā)生在密封止口處,比較明顯的斷裂源有3個(gè),如圖2箭頭所示的A,B,C 3個(gè)部位。
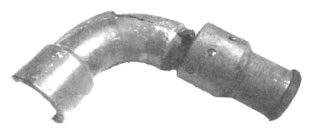
圖1破裂彎頭宏觀照片
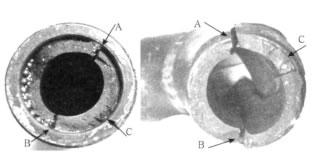
圖2破裂彎頭匹配斷口特征
A區(qū):有一條穿透壁厚的縱裂紋,縱裂面覆蓋一層嚴(yán)重的腐蝕產(chǎn)物,用熱鹽酸水溶液清洗后斷口形貌如圖3所示??v裂面斷口分為2個(gè)較明顯的區(qū)域:靠?jī)?nèi)壁一側(cè)較平坦,放射狀花樣從內(nèi)壁表面向壁厚方向擴(kuò)展,表明裂紋起源于內(nèi)壁;靠外壁一側(cè)斷口較粗糙呈纖維狀,該區(qū)域是最后撕裂區(qū)。同時(shí)在內(nèi)壁表面發(fā)現(xiàn)多條縱向微裂紋,可見該縱裂紋的形成與內(nèi)壁表面微裂紋相關(guān)。
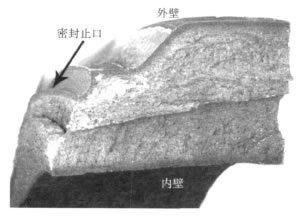
圖3 A部位縱裂縫斷而形貌
B區(qū):與A區(qū)特征大致相同。
C區(qū):該區(qū)約占整個(gè)斷面1/ 5,斷面上有多個(gè)層狀小平臺(tái),平臺(tái)上有明顯的放射狀條紋,條紋收斂于外側(cè)的密封止口底部,該處壁厚較薄。
根據(jù)上述特征可以看出斷裂的發(fā)展順序?yàn)?A,B內(nèi)壁表面微裂紋向縱、橫向擴(kuò)展,當(dāng)擴(kuò)展到一定程度,在C部位密封止口底部產(chǎn)生橫裂紋,最終產(chǎn)生橫向斷裂。
1. 2金相檢驗(yàn)
宏觀檢查發(fā)現(xiàn),圖2所示的A,B部位內(nèi)壁表面有多條縱向微裂紋,磨制其內(nèi)壁表面觀察到裂紋處及其附近有一些腐蝕坑,這些腐蝕坑常萌生于硫化物夾雜處(見圖4)。通過腐蝕坑底取橫截面金相試樣,裂紋呈鋸齒狀沿彎頭厚度方向擴(kuò)展,其內(nèi)有腐蝕產(chǎn)物,尾端??梢娏蚧飱A雜。
取縱截面金相試樣觀察,細(xì)條狀硫化物夾雜頗多(見圖5),按G B/ T 10561- 2005標(biāo)準(zhǔn)評(píng)定為A3級(jí)。
經(jīng)測(cè)量,試樣內(nèi)、外壁滲碳層深度為1. 2一1.4 mm,符合相關(guān)技術(shù)條件要求。
試樣內(nèi)、外壁表層組織均為粗片狀回火馬氏體+殘余奧氏體,原奧氏體晶粒度為8級(jí),裂紋沿奧氏體晶界擴(kuò)展(見圖6),終止于滲碳層內(nèi)部;心部為馬氏體與貝氏體的回火組織。
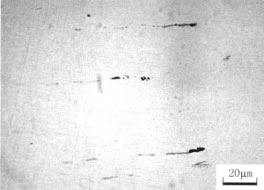
圖4內(nèi)壁表而硫化物夾雜與腐蝕坑
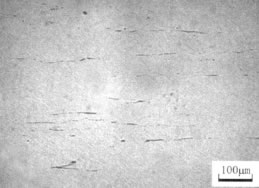
圖5截面試樣硫化物夾雜
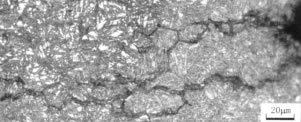
圖6裂紋沿奧氏體晶界擴(kuò)展
1. 3掃描電鏡觀察
用掃描電鏡對(duì)圖2所示的主斷口和A,B部位縱裂面進(jìn)行分析,斷口覆蓋有腐蝕產(chǎn)物,腐蝕產(chǎn)物中富集C1元素(w (C1)=17. 11%)見圖7。
用丙酮溶液清洗去掉主斷口腐蝕物后觀察,彎管內(nèi)、外壁表層(深度約0. 84 mm的范圍)以沿晶斷裂為主,局部有二次沿晶裂紋,顯示出明顯的冰糖狀花樣,見圖8。其余部位為準(zhǔn)解理+解理特征,并有少量細(xì)小二次裂紋。
用掃描電鏡能譜分析儀對(duì)金相試樣進(jìn)行分析,內(nèi)壁表層腐蝕坑內(nèi)除Fe, Si的氧化物外,還富集有氯元素和少量硫元素(圖9);裂紋尾端分叉,其內(nèi)也富集氯元素(見圖10);裂紋尾端硫化物為硫化錳,夾雜中亦富集氯元素(見圖11)。
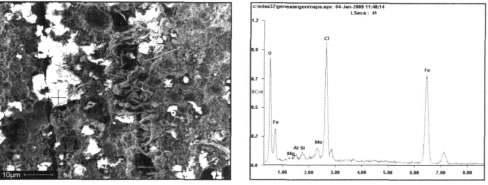
圖7斷口腐蝕產(chǎn)物能譜分析圖
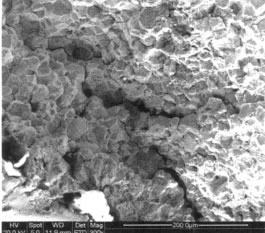
圖8外壁表層沿晶斷口及二次裂紋特征
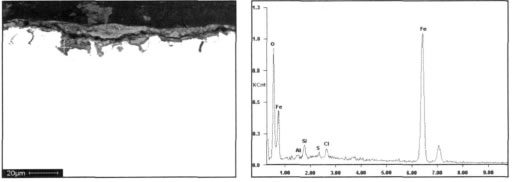
圖9截面內(nèi)壁表層腐蝕坑形貌及能譜分析圖
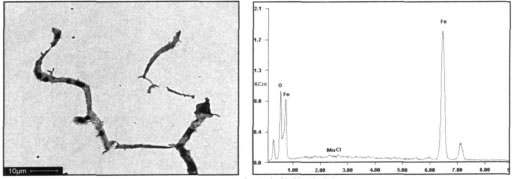
圖10裂紋內(nèi)腐蝕產(chǎn)物能譜分析圖
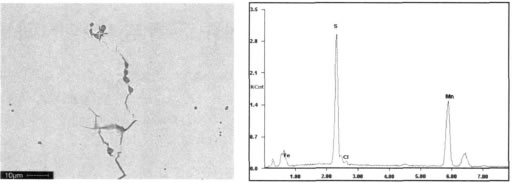
圖11裂紋尾端硫化物夾雜及能譜分析圖
2.結(jié)果分析
根據(jù)上述檢驗(yàn)結(jié)果,可認(rèn)為某油田壓裂車上的活動(dòng)彎頭在壓裂作業(yè)時(shí)發(fā)生爆裂事故,屬于應(yīng)力腐蝕破裂。
應(yīng)力腐蝕破裂是金屬構(gòu)件在拉應(yīng)力(外應(yīng)力或殘余應(yīng)力)和腐蝕介質(zhì)的共同作用下,引起的一種破壞形式。分析引起爆裂的因素如下:
1)掃描電鏡能譜分析結(jié)果表明,在彎頭內(nèi)壁腐蝕坑內(nèi)、裂紋中及硫化錳夾雜處均富集氯元素,沿晶破壞是應(yīng)力腐蝕破壞的一個(gè)特征,這說明引起彎頭應(yīng)力腐蝕的介質(zhì)是氯化物,它是一種很強(qiáng)的應(yīng)力腐蝕介質(zhì)。該活動(dòng)彎頭僅使用1年左右,接觸的介質(zhì)為酸化液(20%的HC1+1.5%的HF+粘合劑),可見氯化物來源于酸化液中的HCI。
2)打一口井的酸化壓裂要壓入的酸性介質(zhì)體積在400 m3到1 000 m3,壓裂的壓力在50 ~ 90MPa之間。因此,活動(dòng)彎頭在工作過程中要承受很大的拉應(yīng)力,為應(yīng)力腐蝕提供了應(yīng)力方面的條件。
3)該活動(dòng)彎頭材質(zhì)為20C rN iMo、其化學(xué)成分、機(jī)械性能均符合有關(guān)標(biāo)準(zhǔn)的要求。金相檢驗(yàn)結(jié)果表明,材料中硫化錳夾雜頗多,按GB/ T 10561-2005標(biāo)準(zhǔn)評(píng)定達(dá)到了A3級(jí)。這表明該鋼的純凈度較差,夾雜物數(shù)量較多會(huì)顯著降低鋼的耐應(yīng)力腐蝕性能。從金相檢驗(yàn)中發(fā)現(xiàn),腐蝕坑產(chǎn)生于硫化錳夾雜處,而裂紋萌生于腐蝕坑底部,可見活動(dòng)彎頭材質(zhì)中嚴(yán)重的硫化錳夾雜是應(yīng)力腐蝕裂紋的誘發(fā)點(diǎn),它是促使應(yīng)力腐蝕、破壞的因素之一。
3.結(jié)語
某油田壓裂車上的活動(dòng)彎頭在壓裂作業(yè)時(shí)發(fā)生爆裂屬于應(yīng)力腐蝕破裂。由于材質(zhì)中存在嚴(yán)重的硫化錳夾雜,在拉應(yīng)力及氯化物腐蝕介質(zhì)的作用下,由硫化錳夾雜處誘發(fā)的腐蝕裂紋進(jìn)一步擴(kuò)展即造成活動(dòng)彎頭破裂。